Ключевые проблемы современного машиностроения
Сложно поверить, но до сих пор каждая третья компания в российском машиностроении сталкивается с отсутствием свежих идей и технологической отсталостью. Недостаток квалифицированных кадров усугубляет ситуацию: по данным союза машиностроителей, только за прошлый год отрасль недополучила почти 20% молодых специалистов. К этому добавим высокую стоимость модернизации — оборудование устаревает быстро, а бюджеты на обновление почти всегда урезаны. Отдельная головная боль — логистика и нестабильные поставки материалов, особенно в условиях меняющихся экономических реалий. Если раньше инженер был универсалом, то сегодня требуются IT-знания, умение работать с большими данными, навыки управления проектами. Много где решаются эти задачи вслепую, без анализа и системности.
Не помогает и тот факт, что отрасль оказывается в тени цифровизации других секторов. Пока ритейл внедряет облачные сервисы, часть заводов до сих пор полагается на бумажные графики смен и ручные планировки производства. Причин много: страх ошибок, сопротивление сотрудников, нехватка информации о выгодах новых технологий. Часто продвижение инноваций тормозится «сверху»: у менеджеров среднее по рынку представление о трендах, а мотивация к переменам страдает из-за постоянной текучки и давления по срокам. Обычно внедрение нового оборудования или переход на цифровые платформы сопровождаются скепсисом и митингами среди коллектива.
Эксперты советуют внимательно рассмотреть проблемы и перспективы машиностроения, чтобы лучше понимать, как отрасль движется сквозь сложности. Частая причина организационных «провалов» — отсутствие долгосрочного плана развития. Всё делается по принципу «заткнуть дыру», что приводит к образованию новых точек риска. Для роста важно не только следить за конкурентами и технологиями, но и смотреть на собственные ошибки открыто: только так появляется шанс на быстрый рывок.
Лучшие практики повышения производственной эффективности
Цифры не врут: предприятия, внедрившие автоматизацию складских процессов и роботов на сборочных линиях, сокращают время производства в среднем на 23%. При этом, автоматизация не всегда требует многомиллионных вложений — часто можно начать с базовых шагов: умные датчики на ключевых станках, программное управление оборудованием, переход на электронные системы учёта. Безусловный тренд последних лет — внедрение бережливого производства. Методика «Lean» пришла из Японии и строится на поиске и устранении потерь. Если грамотно выстроить непрерывное улучшение, то даже на небольшом производстве виден прирост выхода брака и времени простоя в разы.
Один практический совет: заведите на предприятии карту потерь. Буквально на листах бумаги отмечайте, где чаще всего техника простаивает или сотрудники ждут. Через неделю-две на глаз можно будет определить, куда уходят часы и ресурсы. Другая фишка — кросс-функциональные команды: когда специалисты из конструкторского отдела, цеха и IT садятся вместе, часто находятся решения, о которых никто не думал раньше. На одном из заводов в Татарстане после подобных собраний время настройки оборудования сократилось вдвое, просто за счёт пересмотра рабочих смен.
Цифровые инструменты анализа огромных массивов данных позволяют выявлять узкие места в производстве и прогнозировать выход брака. Специалисты советуют учиться работать с Power BI, Tableau или хотя бы Excel-анализом: на выходе — точные отчёты и графики, а не догадки и неструктурированные таблицы. Не забывайте о простых лайфхаках: автоматизация складов через QR-коды, оптимизация маршрутов внутри цеха с помощью GPS-меток, внедрение контрольных датчиков для отслеживания времени работы станков.
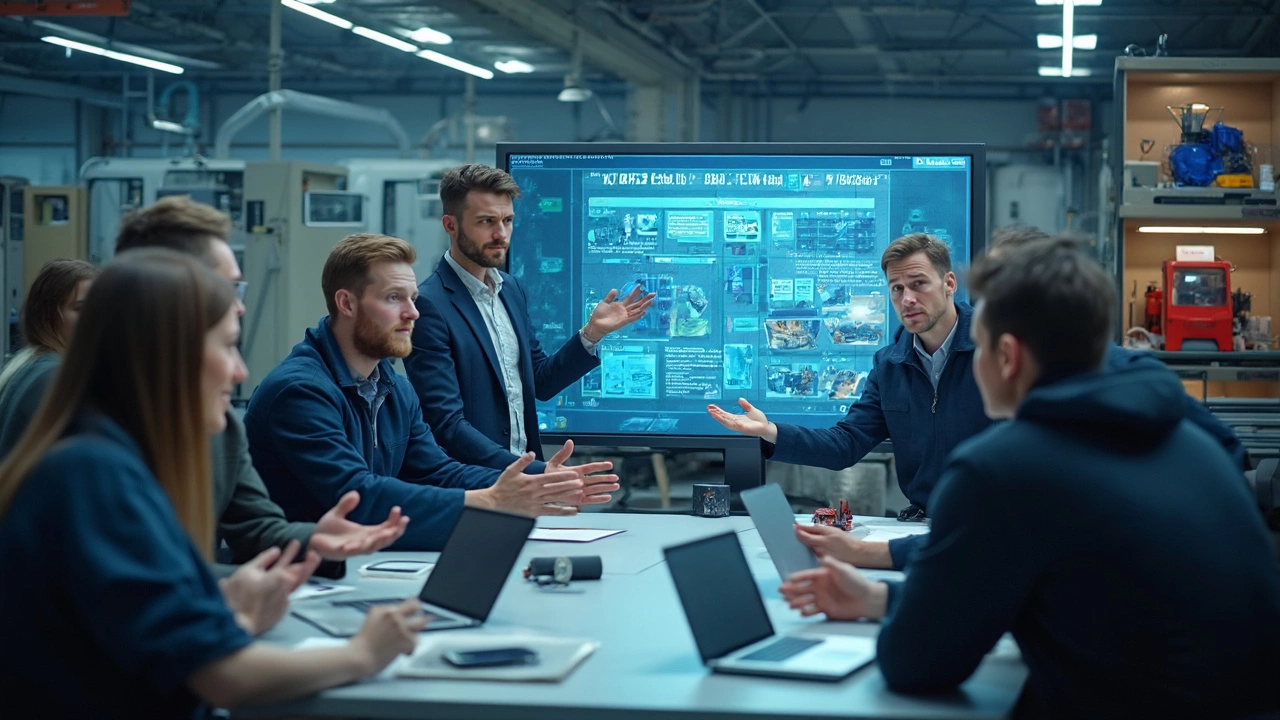
Инновационные технологии как драйвер роста
Если ещё десять лет назад 3D-печать казалась фантастикой, сегодня она доступна даже на средних предприятиях. Компании, которые начали применять аддитивные технологии, сокращают стоимость опытных образцов почти в три раза! А внедрение интернета вещей (IoT) позволяет выполнять мониторинг состояния дерева станков в режиме онлайн, предупреждая аварии и сбои заранее. По статистике Forbes за 2024 год, более 40% ведущих заводов в Европе уже используют IoT-девайсы для отслеживания температуры и вибраций — это снижает риск незапланированных остановок до минимума.
Но не надо бояться слова «инновации». Часто помогают простые решения: стартапы разрабатывают софт для персонального отслеживания производственных показателей, а крупные игроки делятся своими API или открытыми демками для обучения. Специалисты отмечают, что одной из самых быстрых мер роста эффективности стал перевод сервисного обслуживания оборудования на удалённый мониторинг и техническую поддержку в чате. Не тяните с экспертизой: закажите аудит ваших процессов у независимых консультантов или посоветуйтесь с вузовскими экспертами. Очень часто свежий взгляд со стороны открывает неожиданные перспективы для экономии и ускорения работ.
Не забываем об искусственном интеллекте: современные системы на базе AI автоматизируют оценку брака, прогнозируют износ деталей и даже рекомендуют оптимальное расписание производства. По данным портала Statista, такие решения повышают точность планирования на 18% в первый год внедрения. Технологии быстро дешевеют, а внедрение их в конвейер дает не только прорыв на рынке, но и лояльность сотрудников: молодым технологам интересна работа с новым оборудованием, а не рутинная настройка станков.
Мотивация персонала и образовательные практики
Невозможно внедрить инновации и повысить эффективность, если команда не хочет развиваться. Коллектив должен видеть смысл перемен: мотивация строится не только на бонусах, но и на уважении к интересам и идеям работников. Исследования HeadHunter показали, что наличие программы непрерывного обучения увеличивает удержание персонала на производстве на 27%. А позитивная корпоративная атмосфера снижает количество конфликтов и аварийных ситуаций. Секрет в том, чтобы не бояться экспериментов — давайте сотрудникам самим инициировать улучшения, проводите внутренние конкурсы технических решений, поощряйте авторов самых нестандартных идей.
Очень помогает внедрение системы наставничества: когда опытные специалисты сопровождают новичков первые месяцы, не только учат их уникальным приёмам, но и формируют бережное отношение к технике и процессу. Персональные встречи для разбора ошибок — ещё один проверенный инструмент. Вместо окриков на планёрках — разбор реальных кейсов, обсуждение, где и почему допустили промахи, а потом обмен рабочими находками. Важно интегрировать современные образовательные платформы: корпоративные онлайн-курсы, общие чаты для обмена лайфхаками, тренинги по цифровым навыкам.
Небольшой совет: начните с ежемесячных сессий обмена опытом. На таких встречах даже самые застенчивые работники начинают предлагать решения и обсуждать сложности, а у руководства появляется понимание, какие процессы требуют срочных изменений. Формула успеха — верить в людей и не ограничивать творчество. Проверка знаний новыми форматами форума делает обучение не скучным, а вовлекающим.
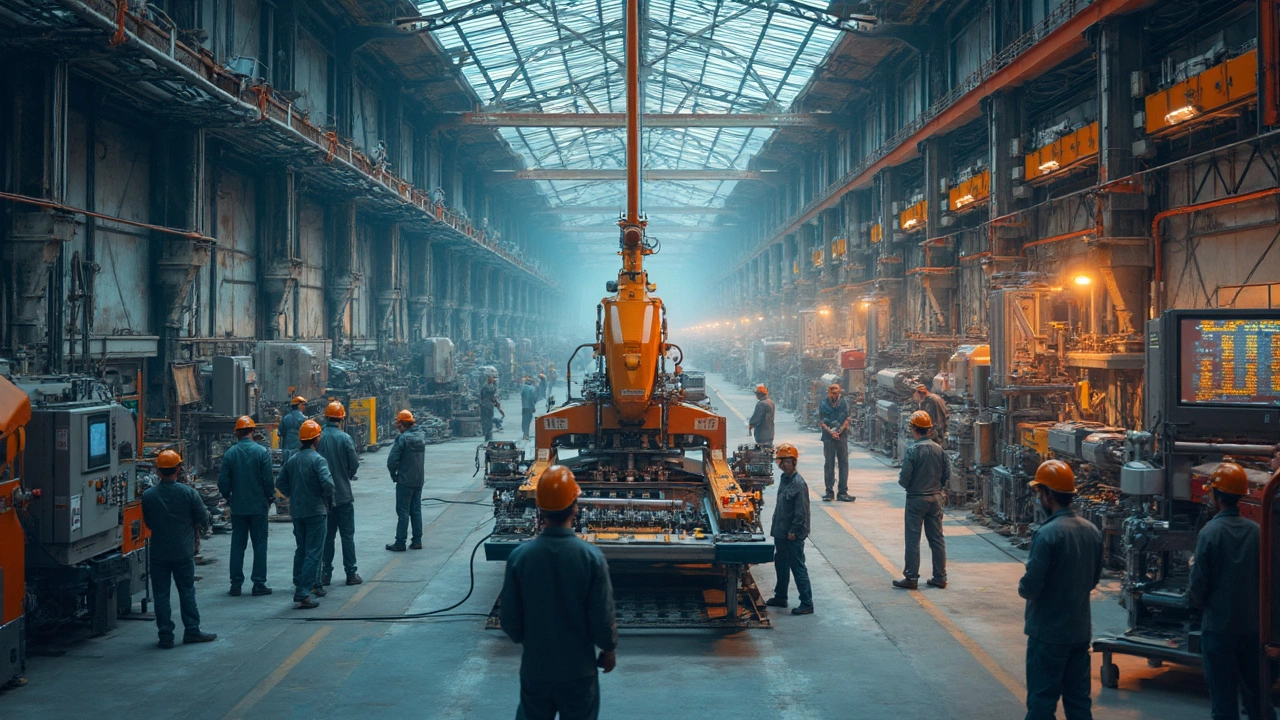
Как внедрять изменения без стресса для компании
Одна из главных ошибок при внедрении инноваций — пытаться сразу поменять всё. Эксперты советуют идти малыми шагами: например, начать с одной пилотной линии, протестировать новый подход на небольшом участке, а потом аккуратно масштабировать на другие цеха. Такой подход легче принимается коллективом и позволяет собрать быстрые отзывы. Для фиксации результата хорошо работают карты внедрения: записывайте, какие изменения были запущены, кто был ответственным, какой результат получили через неделю, месяц, квартал. Рекомендуется выделять так называемых «агентов изменений» — активных сотрудников, которые будут вдохновлять остальных и помогать преодолеть скепсис среди персонала.
Не забывайте про коммуникацию: рассказывайте командам, что происходит, зачем происходят эти перемены, где можно задать вопросы или пожаловаться, если что-то идёт не так. Организация регулярных встреч без галстуков, где обсуждаются новые успехи или проблемы с новыми технологиями, помогает снять стресс и снизить недовольство. Также важно устраивать обмен опытом с другими предприятиями — либо на отраслевых выставках, либо в виде онлайн-встреч. По статистике, компании, которые делают ставку на обмен решениями внутри своей сферы, внедряют инновации почти в полтора раза быстрее.
В конце концов, изменения должны стать частью корпоративной культуры. Маленькие победы — быстрые бонусы, большие изменения — результат терпения и готовности признавать ошибки. Главное — не пытаться быть идеальными на бумаге, а честно прописывать все замечания и дорабатывать до победы в действии. Если следовать этим шагам, внедрять инновации и повышать эффективность не так уж и страшно, зато выгоды ощущаются буквально через пару циклов выпуска техники.